What is Porosity in Welding: Finest Practices for Avoiding Permeable Welds
What is Porosity in Welding: Finest Practices for Avoiding Permeable Welds
Blog Article
Understanding Porosity in Welding: Checking Out Causes, Effects, and Avoidance Techniques
Porosity in welding is a consistent obstacle that can dramatically influence the top quality and honesty of welds. As specialists in the welding sector are well mindful, comprehending the reasons, impacts, and prevention techniques connected to porosity is important for accomplishing robust and reputable welds. By delving into the origin of porosity, examining its detrimental impacts on weld quality, and exploring reliable avoidance methods, welders can improve their understanding and skills to produce high-quality welds regularly. The elaborate interplay of variables adding to porosity calls for a comprehensive understanding and a positive strategy to ensure effective welding results.
Typical Sources Of Porosity
Contamination, in the form of dust, oil, or corrosion on the welding surface, produces gas pockets when heated, leading to porosity in the weld. Improper shielding occurs when the shielding gas, commonly used in procedures like MIG and TIG welding, is incapable to totally shield the molten weld swimming pool from responding with the bordering air, resulting in gas entrapment and succeeding porosity. In addition, poor gas insurance coverage, often due to incorrect circulation prices or nozzle positioning, can leave components of the weld unsafe, permitting porosity to develop.
Impacts on Weld Quality
The presence of porosity in a weld can substantially jeopardize the general top quality and honesty of the bonded joint. Porosity within a weld develops gaps or dental caries that deteriorate the structure, making it a lot more susceptible to fracturing, corrosion, and mechanical failing.
Additionally, porosity can hinder the efficiency of non-destructive testing (NDT) methods, making it testing to spot various other problems or discontinuities within the weld. This can cause significant safety issues, specifically in important applications where the structural honesty of the bonded elements is critical.
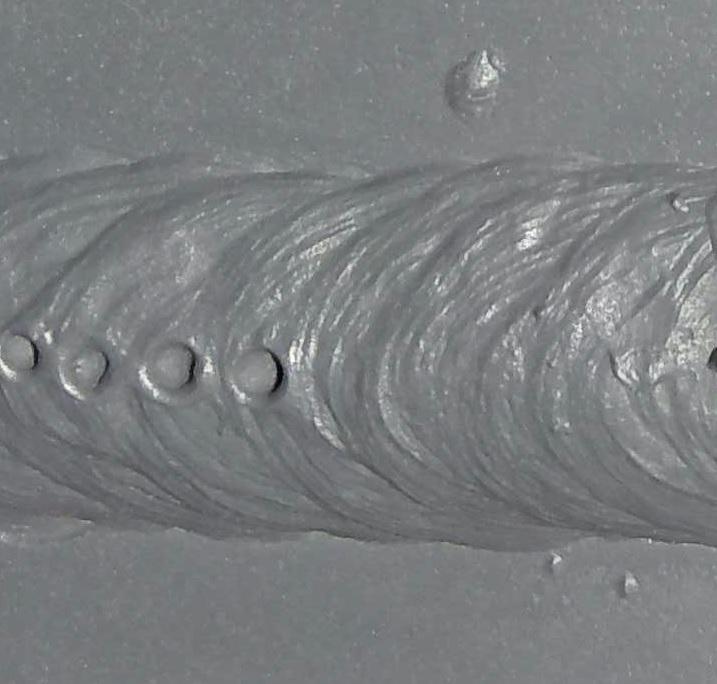
Avoidance Techniques Introduction
Given the damaging impact of porosity on weld top quality, effective avoidance methods are vital to keeping the structural honesty of welded joints. Among the primary prevention strategies is extensive cleansing of the base materials prior to welding. Contaminants such as oil, grease, corrosion, and moisture can add to porosity, so guaranteeing a tidy work surface area is necessary. Correct storage of welding consumables in dry problems is likewise critical to stop dampness absorption, which can lead to gas entrapment throughout welding. Additionally, picking the ideal welding specifications, such as voltage, present, and travel rate, can help lessen the threat of porosity formation. Making sure ample shielding gas flow and protection is an additional crucial prevention strategy, as not enough gas coverage can result in climatic contamination and porosity. Finally, appropriate welder training and qualification are essential for executing safety nets efficiently and continually. By integrating these avoidance strategies right into welding techniques, the event of porosity can be significantly reduced, leading to stronger and more dependable welded joints.
Significance of Correct Shielding
Proper protecting in welding plays a vital role in protecting against climatic contamination and guaranteeing the integrity of welded joints. Shielding gases, such as argon, helium, or a mix of both, are commonly website here made use of to shield the weld swimming pool from reacting with components in the air like oxygen and nitrogen. When these reactive elements enter call with the warm weld swimming pool, they can create porosity, leading to weak welds with minimized mechanical properties.
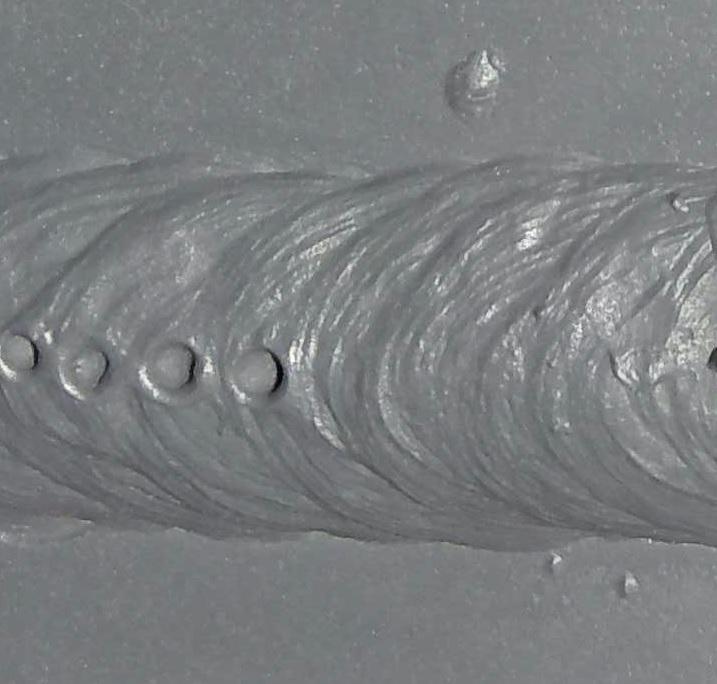
Insufficient shielding can cause various defects like porosity, spatter, and oxidation, endangering the structural integrity of the bonded joint. Adhering to correct shielding methods is essential to create high-quality welds with very little issues and guarantee the durability and integrity of the welded elements.
Surveillance and Control Approaches
Just how can welders effectively monitor and control the welding process to guarantee ideal results and avoid flaws like porosity? By constantly checking these variables, welders can recognize inconsistencies from the ideal conditions and make immediate adjustments to stop porosity development.

Additionally, executing appropriate training programs for welders is crucial for monitoring and controlling the welding process effectively. What is Porosity. Enlightening welders on the relevance of keeping constant specifications, such as appropriate gas shielding and travel rate, can assist avoid porosity problems. Regular assessments and certifications can also make certain that welders are proficient in surveillance and managing welding processes
Furthermore, using automated welding systems can improve tracking and control capabilities. These systems can precisely regulate welding parameters, reducing the likelihood of human error additional info and ensuring regular weld top quality. By integrating advanced tracking innovations, training programs, and automated systems, welders can effectively keep an eye on and manage the welding procedure to lessen porosity defects and attain premium welds.
Conclusion
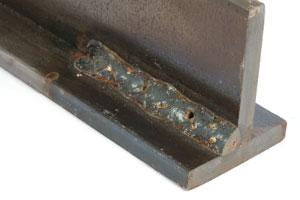
Report this page