What is Porosity in Welding: Recognizing Its Reasons and Enhancing Your Abilities
What is Porosity in Welding: Recognizing Its Reasons and Enhancing Your Abilities
Blog Article
The Scientific Research Behind Porosity: A Comprehensive Guide for Welders and Fabricators
Understanding the detailed devices behind porosity in welding is critical for welders and producers making every effort for flawless craftsmanship. From the make-up of the base materials to the intricacies of the welding procedure itself, a plethora of variables conspire to either aggravate or relieve the visibility of porosity.
Comprehending Porosity in Welding
FIRST SENTENCE:
Assessment of porosity in welding reveals crucial understandings into the integrity and quality of the weld joint. Porosity, characterized by the presence of dental caries or voids within the weld metal, is a common problem in welding procedures. These gaps, if not appropriately dealt with, can endanger the structural integrity and mechanical residential properties of the weld, bring about potential failings in the completed item.

To identify and quantify porosity, non-destructive testing methods such as ultrasonic testing or X-ray examination are often utilized. These techniques permit the identification of internal issues without endangering the integrity of the weld. By assessing the size, shape, and circulation of porosity within a weld, welders can make informed choices to enhance their welding procedures and attain sounder weld joints.

Aspects Affecting Porosity Formation
The occurrence of porosity in welding is influenced by a myriad of variables, ranging from gas protecting effectiveness to the details of welding specification setups. Welding specifications, consisting of voltage, present, take a trip speed, and electrode type, likewise impact porosity formation. The welding technique employed, such as gas metal arc welding (GMAW) or shielded metal arc welding (SMAW), can influence porosity development due to variations in warmth distribution and gas protection - What is Porosity.
Effects of Porosity on Weld Top Quality
Porosity development considerably compromises the structural honesty and mechanical buildings of welded joints. When porosity is present in a weld, it develops spaces or cavities within the product, decreasing the total toughness of the joint. These spaces serve as stress and anxiety focus factors, making the weld a lot more prone to fracturing and failing under lots. The presence of porosity additionally damages the weld's resistance to corrosion, as the trapped air or gases within the gaps can react with the surrounding environment, causing destruction with time. In addition, porosity can prevent the weld's capability to endure pressure or influence, additional endangering the general top quality and reliability of the bonded structure. In critical click here for info applications such as aerospace, vehicle, or structural buildings, where safety and security and toughness are extremely important, the harmful effects of porosity on weld high quality can have serious effects, highlighting the significance of lessening porosity via proper welding techniques and procedures.
Techniques to Reduce Porosity
In addition, making use of the appropriate welding parameters, such as the right voltage, present, and travel speed, is essential in avoiding porosity. Keeping a consistent website here arc length and angle during welding also assists decrease the probability of porosity.

Using the appropriate welding strategy, such as back-stepping or utilizing a weaving motion, can likewise aid disperse warm equally and lower the chances of porosity development. By executing these methods, welders can properly lessen porosity and produce top quality welded joints.
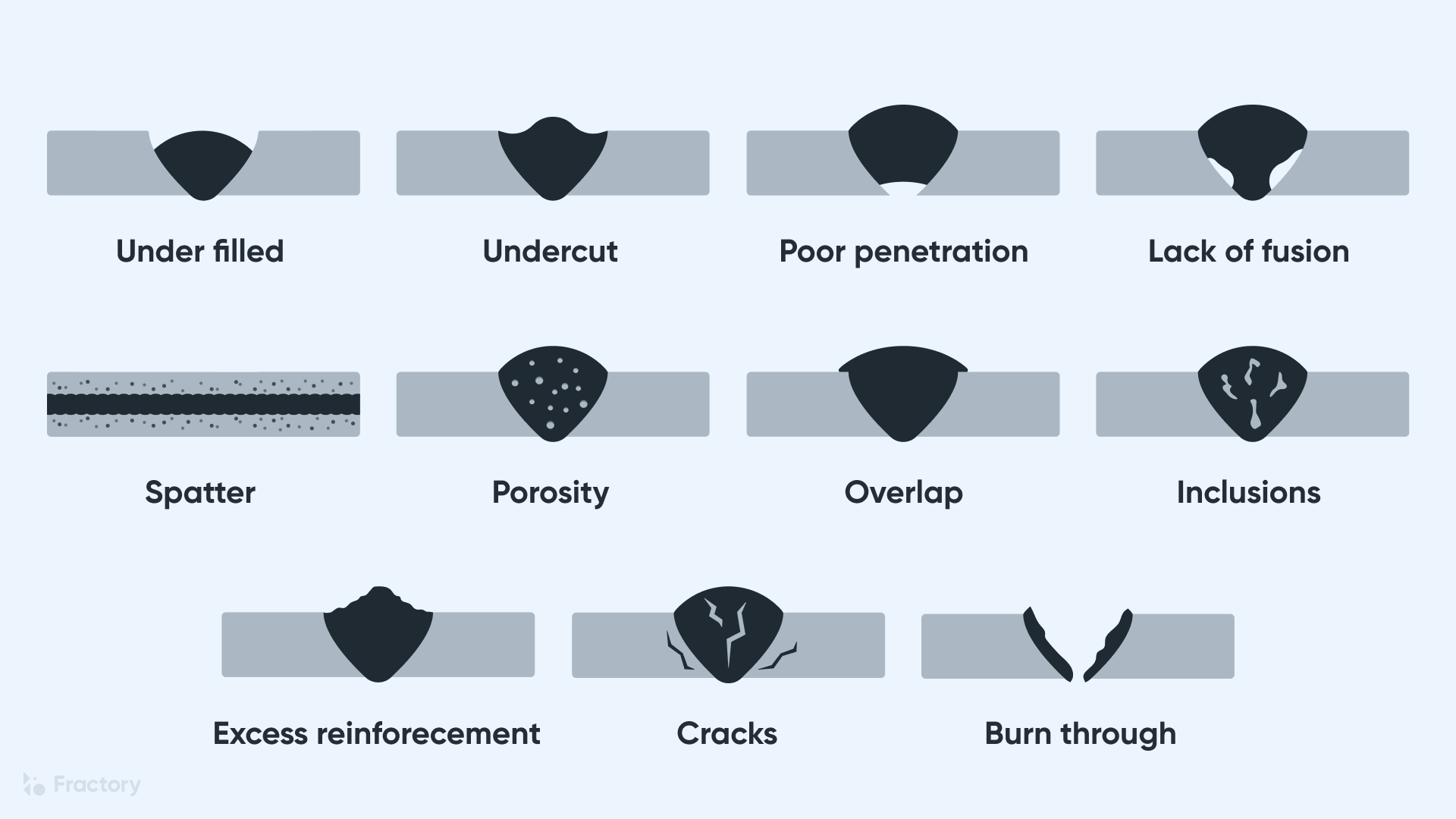
Advanced Solutions for Porosity Control
Carrying out innovative modern technologies and ingenious methods plays an essential role in accomplishing exceptional control over porosity in welding procedures. In addition, utilizing advanced welding strategies try this such as pulsed MIG welding or changed atmosphere welding can additionally assist reduce porosity problems.
Another advanced remedy entails the use of advanced welding equipment. For example, using devices with integrated attributes like waveform control and sophisticated source of power can boost weld quality and decrease porosity threats. The implementation of automated welding systems with exact control over specifications can substantially lessen porosity defects.
In addition, incorporating innovative surveillance and inspection technologies such as real-time X-ray imaging or automated ultrasonic screening can help in detecting porosity early in the welding procedure, permitting prompt corrective actions. Generally, integrating these sophisticated remedies can significantly boost porosity control and boost the overall high quality of welded components.
Verdict
In conclusion, comprehending the scientific research behind porosity in welding is crucial for welders and producers to produce top notch welds - What is Porosity. Advanced options for porosity control can further improve the welding process and ensure a strong and reputable weld.
Report this page